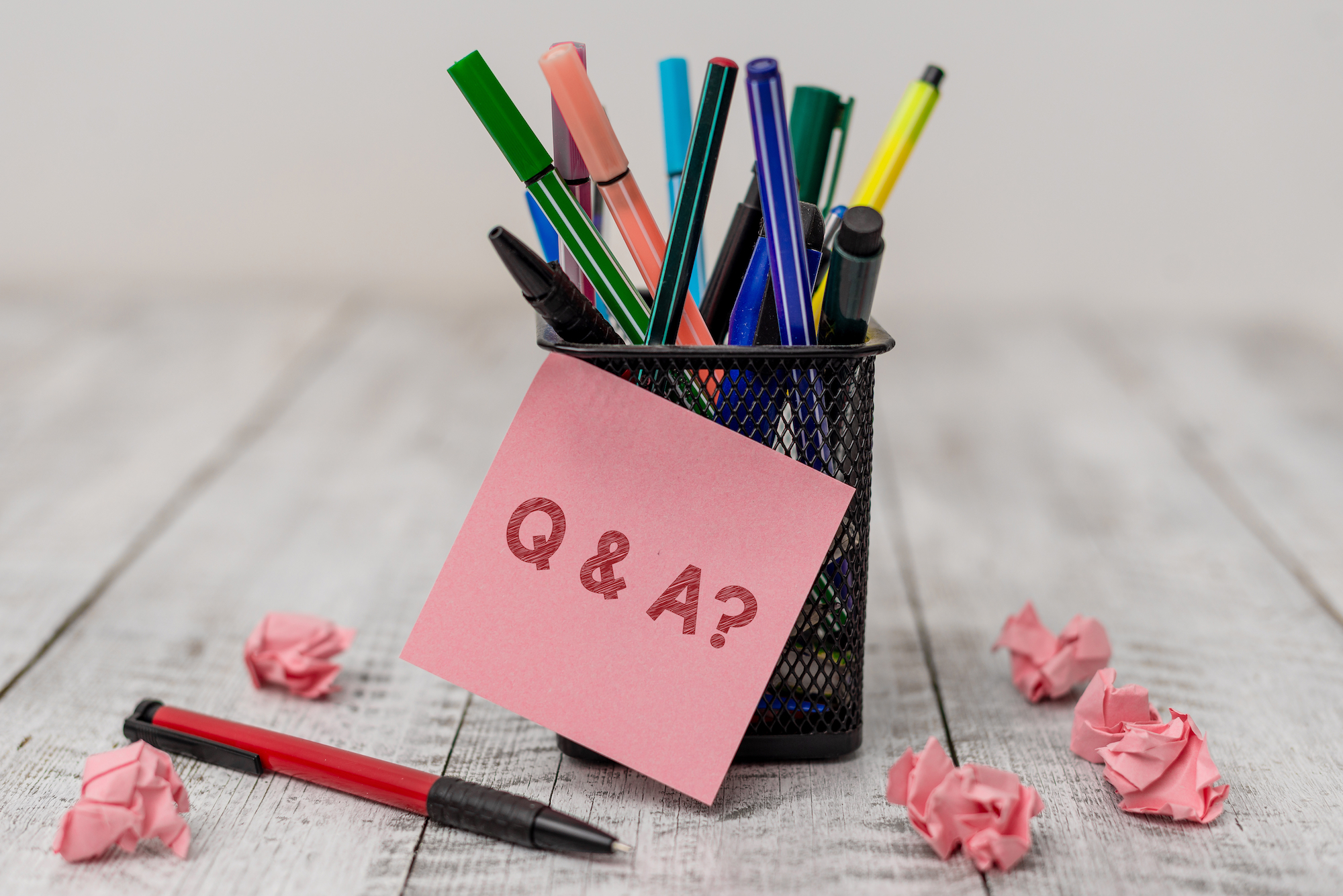
We’ve heard a lot of great questions about the product development process with more folks using the pandemic shakeup as an opportunity to make their ideas come to life. As 2020 comes to a close, Enventys Partners reflects on our most common prototyping and manufacturing questions of the year.
Top Product Development Questions (and Answers) of 2020
For many, 2020 has been a year to forget. The pandemic and its fallout have upended life as we knew it, creating challenges for populations that span across social lines and international borders.
The silver lining in all the chaos is that these challenges, both small and immense, have only boosted the collective creativity that we humans share.
Folks are using the COVID-19 shakeup to take the ideas that have been rolling around in their heads and finally make them real. As a result, I have heard a lot of good questions about the product development process. To cap off the year, here are the answers to some of the best product development questions from 2020.
1. How much does it cost to patent an idea and how long does it take?
Filing a patent is often a crucial part of the inventor’s strategy since it gives them the exclusive rights to the technology for many years. There are two main types of patents in the United States: design and utility. The differences between them are their costs and timelines.
Utility Patents
Valid for twenty years after the date of filling, utility patents encompass the core technology of the invention. Since utility patents cover raw engineering, the timeline and cost to file can vary depending on the complexity of the concept. In broad strokes, it is about $2.5K-10K, including lawyer fees, and takes approximately two years to obtain. However, the USPTO does offer expedited services that can cut the time in half, but this comes with additional fees.
Design Patents
Design patents cover only the aesthetic or ornamental aspects of a product such as the shape of a Coke can or the body design of a Porsche. They are valid for fifteen years (instead of twenty) because they are generally seen as weaker intellectual property. The cost to file a design patent is about half that of a utility patent and it takes about a year to obtain.
Secure Legal Counsel
The actual fees collected by the USPTO for filing a patent are much less than the cost mentioned above. However, the inventor must create the documentation themselves, so we strongly recommended securing legal counsel. This is to make sure filling is done correctly and to lock in the best protection for your technology.
2. What rapid prototyping equipment should I invest in for my home space?
It’s a great help to have rapid prototyping (RP) equipment at home when developing prototypes. It speeds up the process and can save valuable time and money. However, it can be overwhelming to decide which RP technology to use since there are many types with varying capabilities.
3-in-1 Machines
Fortunately, many equipment manufacturers make 3-in-1 machines that can 3D print, laser cut and CNC mill. While providing immense flexibility for the at-home inventor, these machines use motion bases with detachable heads for each of their three functions.
Snapmaker
Snapmaker machines are my favorite 3-in-1 because they require minimal assembly and come with free software. They are the perfect size for desktop manufacturing and gives the inventor more control over their materials and processes. Snapmaker’s 1.0 model starts at $799 and has a working area of 125mm in each axis. If you want something with more bells and whistles, the 2.0 lineup offers additional upgrades and a larger bed size. Starting at $1,199, this lineup will begin shipping in 2021.
3. Why are there minimum order quantities for manufacturing?
Minimum order quantity, or MOQ, is an industry term for the fewest amount of something that you are allowed to order from a manufacturer. Any prototyper knows that it can be extremely difficult to make one of anything. Not only does it take time to design and vet the part, but the machine to make it must also be created. In manufacturing, it’s equally difficult to make one or just a few of any one part.
MOQs Vary Greatly
In order for the manufacturer to achieve their desired return on investment of time, space and capital to build your product, they will require a commitment from you to purchase a certain volume of that product. MOQs will vary from one to millions depending on the part being made and the capabilities of the manufacturer.
Processes with No Tooling
It is common for processes that do not require tooling, like machining and 3D printing, to have low MOQs. In these cases, many shops are happy with an MOQ of only one unit since the time and resource burn is fairly low with these technologies.
Tooled Processes
When you consider tooled processes, like injection molding, MOQs usually start in the thousands. Molding processes require tools to be cut and verified, time on expensive machines that already have production schedules, and raw materials to be purchased in bulk. All of this combined necessitates a heavier purchase commitment.
4. Has the pandemic changed how you approach the development process?
The pandemic has certainly provided a spark for innovation, but it also has forced us to rethink how we as developers do our jobs. While the process for bringing ideas from concept to production has not changed, the execution has.
Collaboration at a Distance
The biggest challenge is maintaining a collaborative process among our team members while being physically apart. It is important to have multiple eyes from both industrial designers and engineers throughout the process to ensure each design is executed at a high level.
Online Communication Tools
Of course, video conferencing tools have been helpful when sharing CAD and live videos of prototypes. We also use WiFi development boards on our electronic projects so engineers can see live data from remote locations.
Small Hands-on Team
However, full virtual collaboration is not a holistic strategy when designing physical components. There’s just so much to learn from touching and using prototypes so engineers must evaluate prototypes in real life. To facilitate this, a small core team is in our shop most days building prototypes, setting up equipment and remote workstations as well as running the rapid prototyping equipment. When parts are ready, they’re shuttled to the project leads’ homes for evaluation. This allows the team to stay as remote as possible while maximizing facetime with the prototypes.
Get Help from Enventys Partners
If you need help bringing a product to life in 2021, reach out to Enventys Partners. Our full-service capabilities allow us to handle every step of the process completely in-house, from research and design to manufacturing and marketing.
Work With Us
Want to learn more about how we’d prepare your product for launch? Request a quote today.
Want To See This Advice In Action?
Check out our case studies and learn more about how we’ve achieved stellar results for our clients.