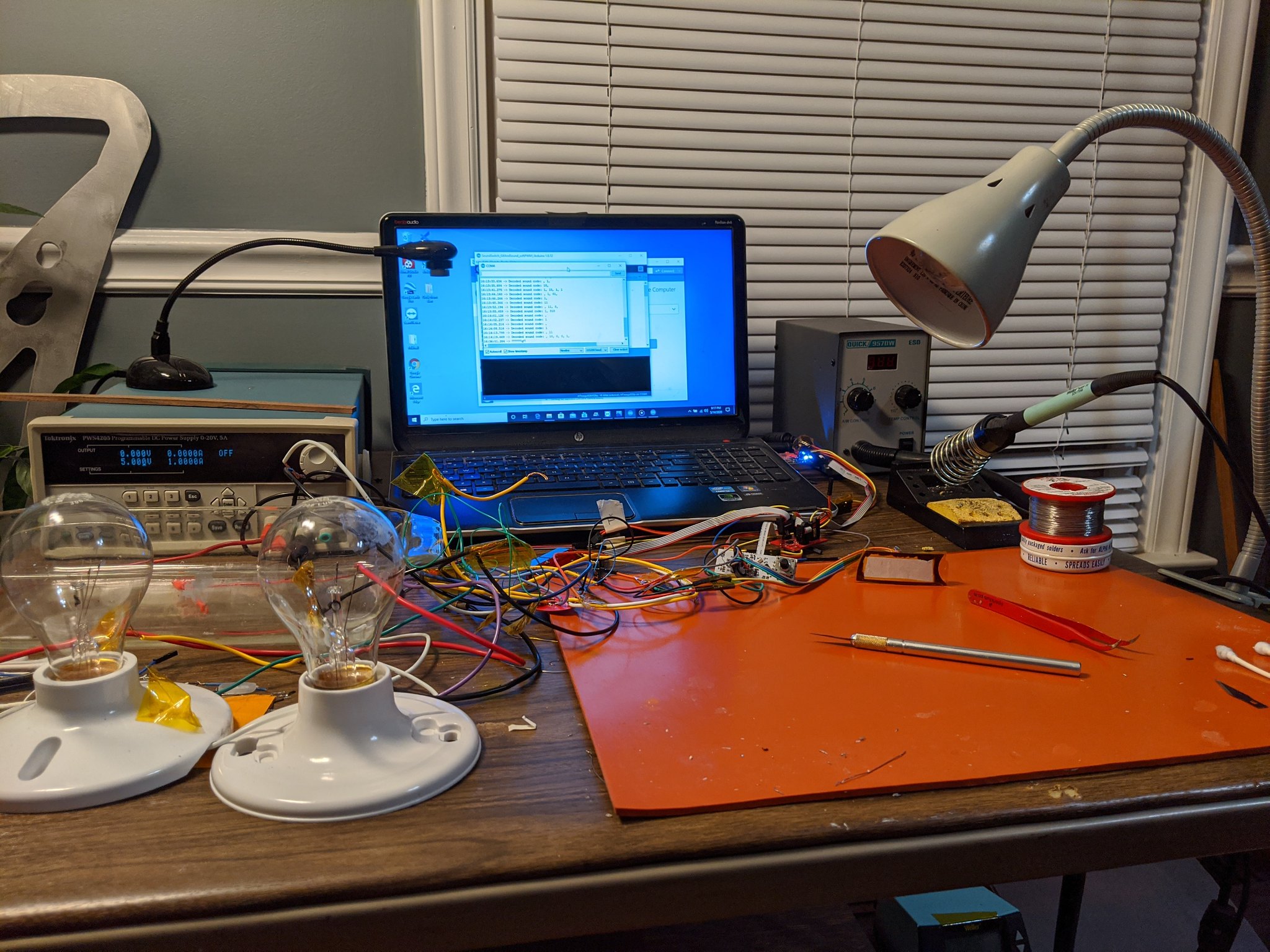
Across the world, businesses, both essential and non-essential, are adjusting to a new normal. While the Enventys Partners Marketing team seamlessly switched to work from home, our Product Development department faced a bit of a quandary. Through agility, initiative and creativity, the staff has figured out ways to continue operating under these unique circumstances.
Prototyping during COVID-19
On March 26, as the coronavirus’s impact had become widespread, Mecklenburg County, where Enventys Partners is located, issued a stay at home order. Since this day, our team has had to incorporate social distancing into our operations, causing us to rethink how we build prototypes entirely.
Non-Essential Shutdown
Initially, the engineering staff was working remotely, when it made sense, but kept the prototyping shop open so we could continue using our tools. However, when all non-essential businesses were set to close, we had to shutter the entire headquarters, including the prototyping shop. No matter how important we are to our clients and the innovation community, Enventys Partners is on the non-essential list.
A New Product Development Process
In just two days from hearing the official news, the engineering team already had a plan to continue prototyping while sheltering in place. At first, it was stressful figuring out how we would effectively design, build and service without the shop. However, looking back on the last seven weeks, our team has shown success in running development programs and building exceptional prototypes. Bringing the tools and techniques from the shop into our homes, here are some processes we’ve adapted during the pandemic.
3D Printing
When people think of prototyping, they often think of 3D printing. While it’s not the only way to build parts, 3D printers have become essential to prototyping and are even being used to create mass-produced pieces. In the last decade, a plethora of desktop 3D printers that use spools of plastic filament has come onto the market. While we use these at Enventys Partners for some applications, most of our needs require high-fidelity parts made on professional-grade printers.
Origin One
Just one week before the shutdown, we commissioned a brand new 3D printer called Origin One. The Origin uses a technique called Programmable Photopolymerization, which prints with photocured resins like a stereolithography machine. Not only does it run parts fast, but materials can be changed quickly, making it well suited for printing at scale. Additionally, unlike most other manufacturing-grade printers, the Origin is relatively small and can easily fit on a desktop.
Operating at Home
Having come to Enventys Partners just in time, it’s size makes it perfect for at-home operation. One of our engineers, TJ Root, volunteered for the challenge, relocating the printer as well as the cleaning equipment to his place. Since setting up was quick and straightforward, we were only without printing capability for a day. Now, when anyone on the team needs parts, they send the file to TJ and pick them up at his house the next day. All in all, the scale and quality of Origin One have allowed us to be flexible, ensuring we never lacked 3D-printed parts.
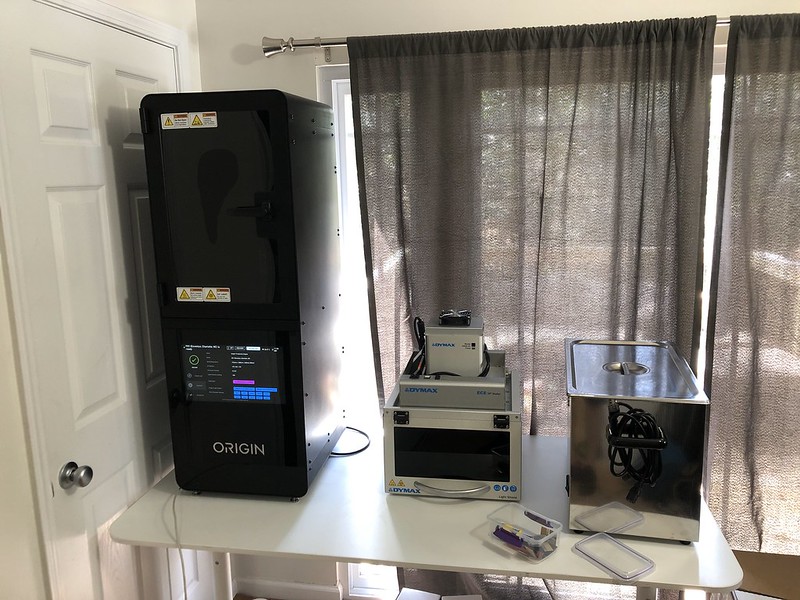
Our new Origin 3D printer and wash station set up at home.
Electronics
Since approximately 75% of our development portfolio is electrified, it was crucial for our team to service those prototypes. Electronic prototypes require populated circuit boards, firmware writing, which is the code that runs on the microcontroller, as well as system testing and troubleshooting.
Circuit Board Assembly
Assembling printed circuit boards, or PCB, remotely turned out to be an easy task. The process includes these steps: our electrical engineer designs the circuit, we order five to ten designs from a PCB board house, then we populate them with components from the Enventys Partners shop. Fortunately, we can manufacture unpopulated boards without skipping a beat because our PCB vendors were all deemed critical businesses and never shut down. Next, when we need unique components, usually for initial prototypes, we purchase them from one of the big supply houses in the US, such as Arrow, Digikey, or Mouser, all of which stayed open as well. Lastly, both the components and the PCBs are sent to our electrical technician’s house for assembly. After taking home a few pieces of specialized equipment from the shop, our tech has been building all of our circuits from his personal workbench, keeping our prototypes running.
Programming and Troubleshooting
While we didn’t have a slow down in circuit board production, the challenge came with programming and troubleshooting electrical prototypes. Since our engineers can write code anywhere, what proved tricky was merging the code with the circuit.
Remote Workstations
Ultimately, we found remote workstations to be most effective when programming and monitoring prototypes, especially since our lead electrical engineer opted to shelter in place in Colorado. First, the lead mechanical engineer on a project takes the circuit home along with the necessary power supplies and wiring. Then, they set up a laptop with the circuit connected via a USB programming cable and a remote access program. This allows our electrical engineer to take control of the computer and interface with the hardware directly. Once the program’s uploaded, the mechanical engineer runs tests, and then the team iterates from there. This technique has allowed us to deliver several electronic prototypes throughout the lockdown.
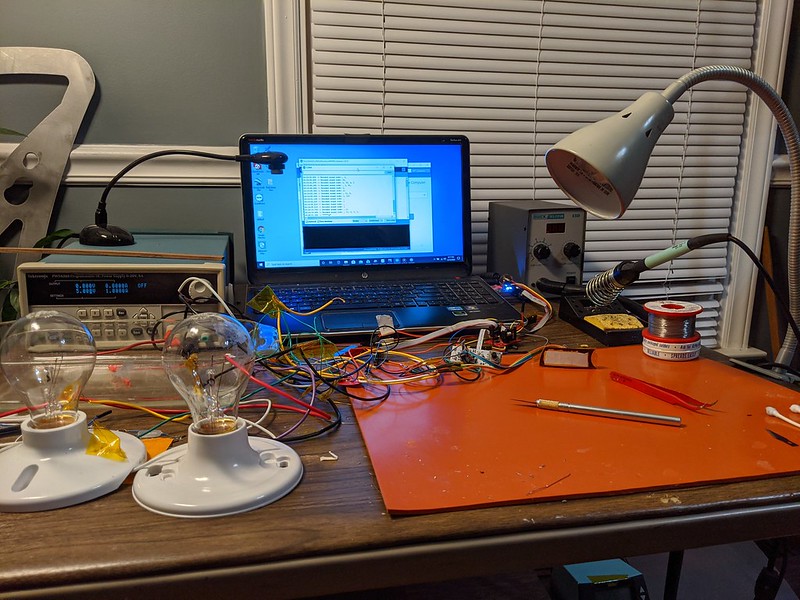
A home-based remote programming station with the necessary equipment to develop prototype electronics.
Physical Prototyping
Beyond 3D printing, we use several other techniques to build prototypes, all of which have been reimagined to accommodate social distancing.
Engaging With Vendors
One remote method of building prototypes is to engage more with vendors. In the past, we’ve asked vendors to help build parts and pieces that we could not make in house, either because we didn’t have the capability or the time. Now, over the last few weeks without access to our equipment, we have relied more heavily on this vendor network to machine or mold our parts.
Making It Ourselves
Fortunately, since the Product Development team is a group of makers themselves, we all have our own decent set of tools. While custom parts are built and shipped to us by vendors, other components can be made from our homes. We knew we were going to mold some prototype parts before the shutdown, so our shop technician brought home the pressure pot and other special molding equipment. Additionally, our team has also been doing paintwork at home, like myself—I’ve touched up airbrush work in my driveway.
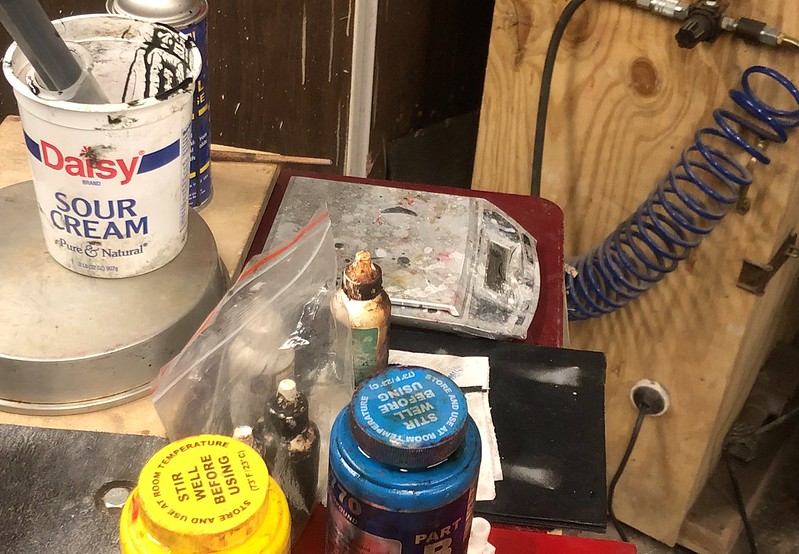
Our technician, Chris Gabriel, set up this ad hoc molding station to accommodate the stay from home order.
Staying Agile During the Pandemic
Prototype building is a remarkably intimate process because, as designers, we must assemble products ourselves to make them the best they can be. Even throughout the COVID-19 crisis, our Product Development department has found ways to stay hands-on, while working remotely, to develop impressive prototypes. Despite the rest of North Carolina starting to open back up, our team will continue working remotely to stay safe, innovating our new operating process as needed. Reach out to Enventys Partners if you need product development assistance—our team of experts is always here to help, even during this season of social distancing.
Work With Us
Want to learn more about how we’d prepare your product for launch? Request a quote today.
Want To See This Advice In Action?
Check out our case studies and learn more about how we’ve achieved stellar results for our clients.