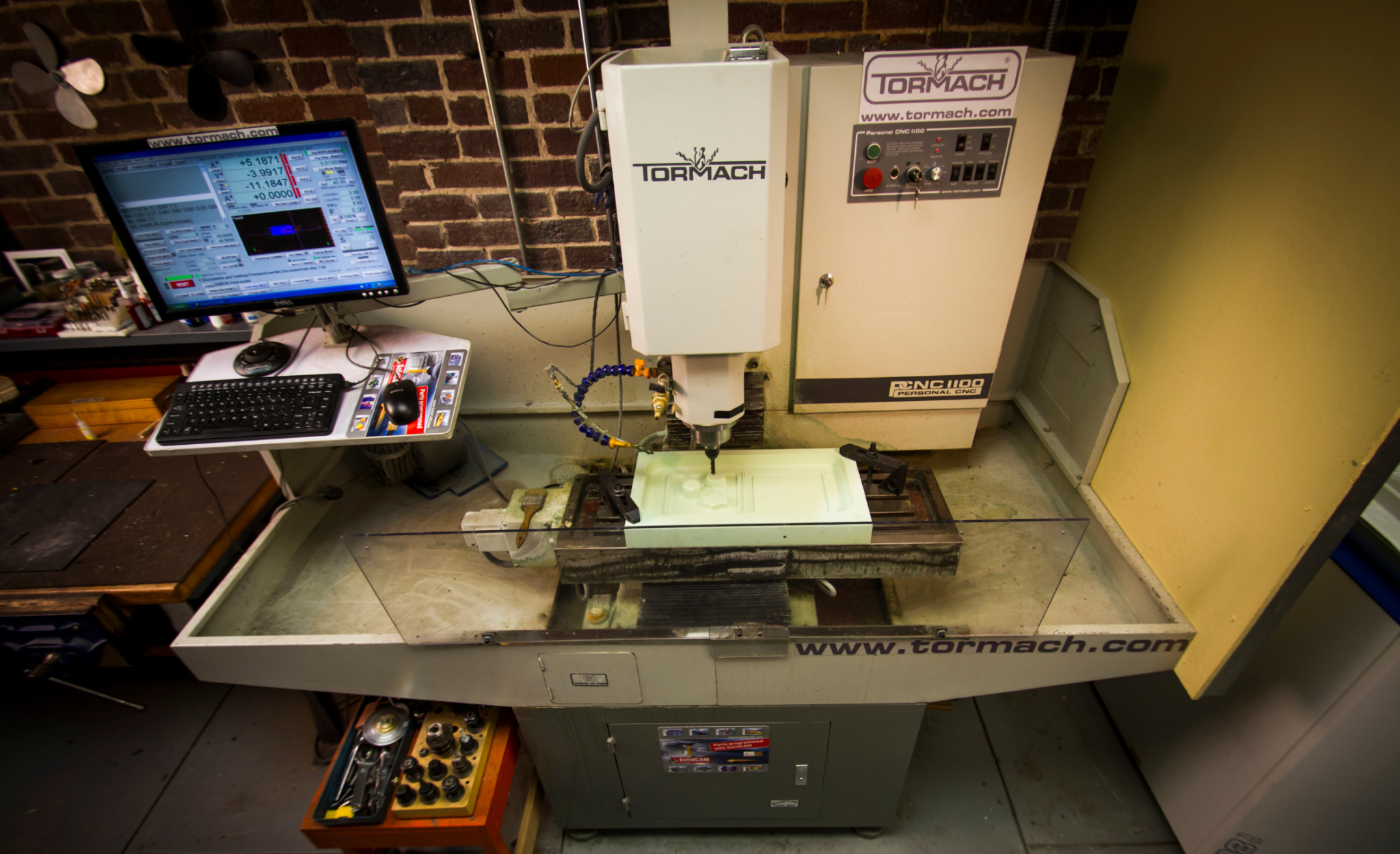
When developing a product, making sure it consistently functions as intended is crucial. There are countless products that rely on consistent material properties and consistent dimensions for the product to function properly.
Traditionally, you would CNC mill a prototype of your design when you reach a point where further validation of your idea can only be achieved through physical testing. While CNC milling prototypes allows you to choose materials very similar to what you would use in production, it can be very expensive and time-consuming.
With recent advancements in 3D printing, it has become the preferred method of prototyping a design. 3D printing removes several limitations that CNC milling has, can be just as accurate, is almost always cheaper and is almost always faster. 3D printing does offer fewer options for mimicking your production materials, but innovation in this sector is happening at such a rapid pace that this should be less and less of an issue moving forward.
Another option for testing is 3D modeling. 3D modeling programs such as SolidWorks let you simulate outside forces on your design but require massive computing power and lots of time to run simulations on large, complex designs. Depending on your simulation set up, these results can be inaccurate or difficult to interpret.
Quality Control During Manufacturing
Once you have used your prototypes to validate that your product functions as intended and you have made sure it’s manufacturable, your product is ready for the tooling phase, assuming you’re going the route of injection molding. There are many things that can go wrong with your parts’ material properties and shape from here, so quality control is very important.
A majority of injection-molded plastics will shrink three to five percent after cooling from a molten state into a hard plastic. This can cause parts to warp and distort, which can make features that are critical to the function of your product ineffective. Tooling designers accommodate for this by making the molds slightly larger than the part you design, and they usually need to be made aware of the material you intend to use so they know exactly what the shrink rate will be.
Design engineers will also provide the manufacturing site with a set of inspection drawings of the parts that can be used to inspect a certain percentage of the parts after injection molding. Parts will need to be inspected for accuracy throughout production, even if they are found to be initially accurate. This is because a number of things can change over the course of a production run. For example, molds can get worn down over time depending on their materials. Aluminum molds will wear down much faster than steel molds, but they are cheaper to make if you don’t plan on molding lots of parts over a long period of time. This wear and tear can cause dimensional accuracy to slip.
The state of the materials used is also difficult to keep consistent, as well as the environment they are being molded in. For example, if you start molding during a humid summer and keep molding through a dry winter, adjustments to molding parameters might need to be made to keep parts consistent. The moisture content of the plastic could go up or down, which can affect material properties, or the ambient temperature around molding machine could change and cause the parts to cool down differently and warp.
Bottom line: creating and testing prototypes to validate your design and monitoring tooling for quality control are two things that can’t be skipped over or done poorly. To learn more about how Enventys Partners can assist with prototyping and manufacturing, get in touch today.
Work With Us
Want to learn more about how we’d prepare your product for launch? Request a quote today.
Want To See This Advice In Action?
Check out our case studies and learn more about how we’ve achieved stellar results for our clients.