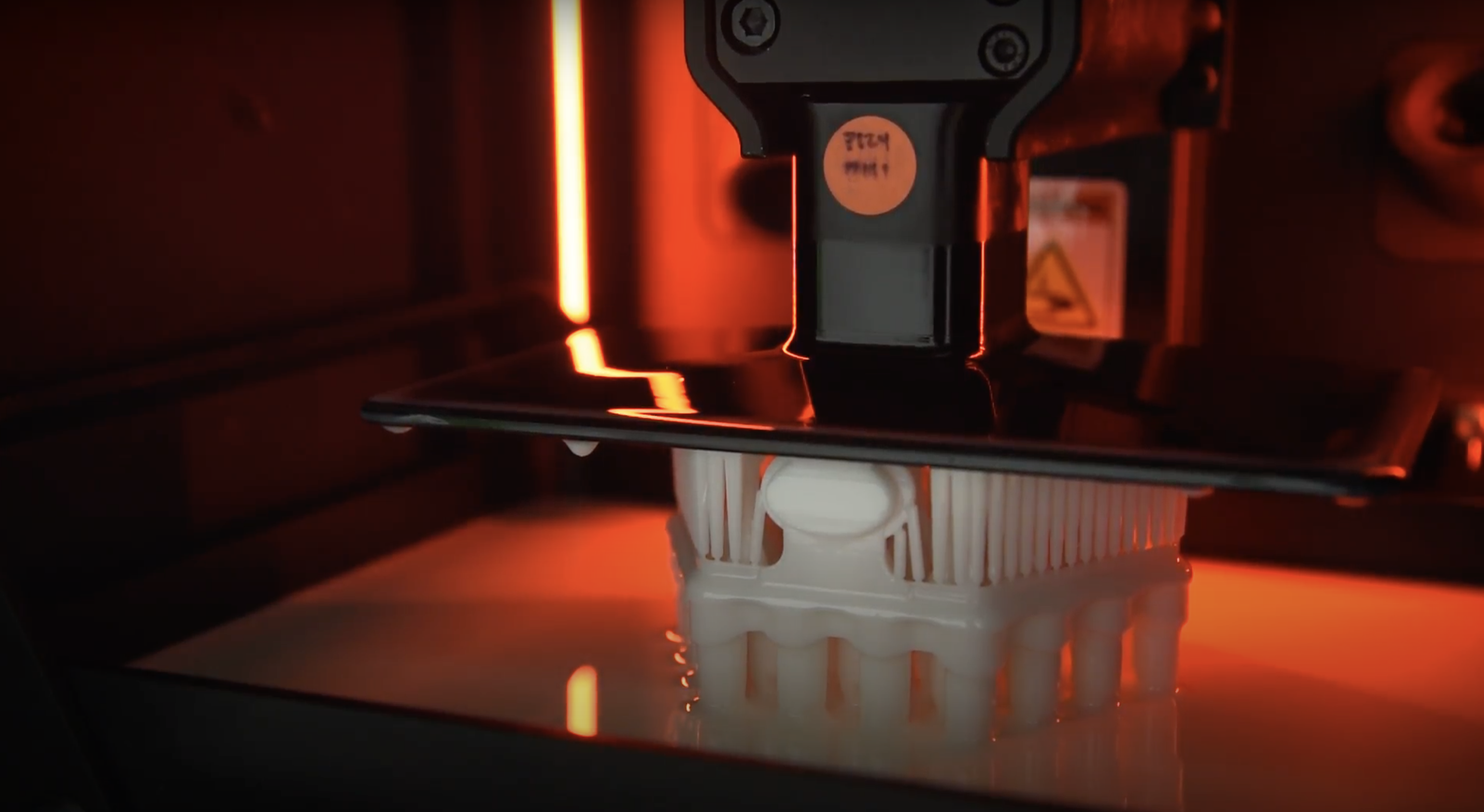
When designing a new product, there comes a point at which the design has to move from paper (or computer screen) to something tangible. It’s a process full of big steps. It’s often expensive, too. Here’s why you should consider additive manufacturing for your next product, and 5 benefits to keep in mind.
Building a product? Consider these 5 benefits of additive manufacturing
Almost every product begins its life as a prototype before hitting the manufacturing line. The process can be arduous and expensive, but what if it could be simplified and streamlined? What if you could prototype and manufacture a product using the same machine? The creation of 3D printers in the 1980s gave some designers the ability to create initial prototypes in a new, incredibly rapid way. As the technology has improved, many manufacturing, design, and development firms have turned to 3D printing as a way to bring more advanced concepts to life – all the way to end-use manufacturing.
These days, when 3D printing is done on a large scale, it’s generally referred to as additive manufacturing (AM, for short). But the underlying technology is exactly the same.
Unless your concept requires a very large quantity of parts, additive manufacturing may offer benefits over traditional manufacturing methods.
1. Time to Market
Traditional manufacturing methods, like injection molding, can take months or years to get from sketch to production. Each part must be designed, prototyped, sent off to have molds constructed, and then finally be produced. Most design tweaks or edits—even very minor ones—require a re-tooling or re-molding of the entire part. This adds significant cost and time delays.
If a prototype created through additive manufacturing reveals a design issue, it can be tweaked and re-printed on-demand with almost no extra work. This speeds the time to market significantly by eliminating the back and forth involved in tweaking very expensive injection molds.
2. Upfront Cost Reduction (Avoiding Tooling Costs)
As 3D printing technologies have evolved, the costs associated with leveraging them have diminished. For low-volume manufacturing projects, this reduced cost makes additive manufacturing an ideal option to consider.
AM boasts a reduction in upfront costs compared to traditional manufacturing methods because the entire process is generally achieved using a single machine. One design is given to one machine, and any iterations are handled in near real-time. For small-volume or very intricate parts, the costs associated with traditional molding can be astronomical. Most products require investing in more than one tool and the costs can compound quickly. Additive manufacturing methods slash those costs dramatically, as your costs are really only for the parts produced.
3. Design Freedom
Conventional manufacturing methods are just that. Conventional. Additive manufacturing offers designers and developers the flexibility to think creatively when manufacturing parts because the technology allows for significantly more freedom. Parts with complex geometries, intricate textures, or other unusual features are more easily designed and produced with an additive-first approach, as opposed to traditional tooling and molding methods.
Recently, Enventys Partners used the Stratasys Origin One printer to design, prototype, and manufacture an innovative head lice treatment device for FloSonix. During the process, our designers seized an opportunity to add a simple feature that would greatly improve the user’s experience with the product. This feature wasn’t part of the functional design of the product and would have been an expensive change using traditional tooling. With AM, our team simply made the change.
4. Staged Development
Because traditional tooling is expensive, and changes can be equally so, a major benefit to additive manufacturing is the ability to develop a product in stages. It’s easy to focus on one aspect of a product at a time, making changes, and printing them in real-time. Staged development allows engineers and designers to fine-tune specific parts of a product without compromising timelines or incurring additional tooling costs.
5. On-Demand Manufacturing
Leveraging the same machine to prototype and manufacture a product has significant benefits. Not only can you be assured that the quality of the final part would match expectations, but you can adjust manufacturing quantities on-demand. Especially for smaller-to-midsize order quantities, AM provides the ability to produce inventory when needed. Minimum order sizes for products produced with additive manufacturing are 10 to 100x smaller than traditional MOQs and lead times for the production are measured in days, not months. You won’t need to worry about carrying costs or logistical nightmares associated with surplus supplies and storage.
Is Additive Right for Your Project?
At Enventys Partners, we evaluate every project uniquely to determine the best way to prototype and manufacture it, from start to finish.
One of the tools we consider is our Stratasys Origin One 3D printer. Chris Prucha, co-founder of Origin, said the following about Enventys Partners’ approach to additive manufacturing on a recent project:
Enventys Partners’ approach to this application is incredibly innovative and an ideal process for any brand taking a complex mid-volume product to market quickly and economically. By using an additive first approach, combining parts, designing custom textures, and taking advantage of Origin One’s material selection and final part quality, they’ve created a playbook for product development using additive manufacturing.
Ready to get started? We’d love to learn more about your idea and help bring it to life.
Work With Us
Want to learn more about how we’d prepare your product for launch? Request a quote today.
Want To See This Advice In Action?
Check out our case studies and learn more about how we’ve achieved stellar results for our clients.